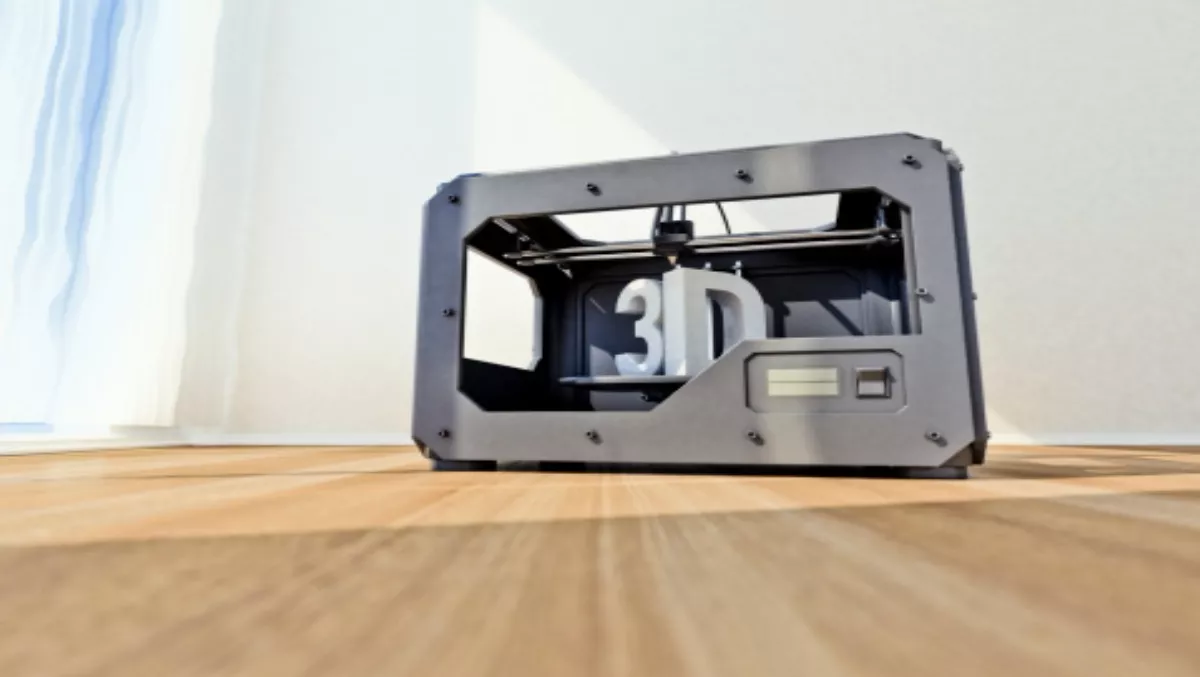
3D printers to build data centres?
With many global brands such as Nike and Ford using 3D printing to help develop and make products such as football boots and brake pads, it is no surprise that tech industries are applying 3D printing to data centers.
An American company called 'IO' is currently using a 3D printer to prototype 'data center modules' , according to Wired.
These are massively complex containers of computing equipment that can be pieced together, to form larger data centers. Similar to other brands IO can shape, test and reshape with ease,
“It allows us to have a much more agile - and fast - process,” says Andreas Zoll, IO’s vice president of engineering.
The idea of a modular data center took root at Google about a decade ago. These are basically shipping containers pre-packed with all the necessary computing, electrical, and cooling equipment, all configured to operate in harmony.
Whether by train, boat or truck, Google could move these containers to locations around world and then piece them back together. It was a way of both streamlining the construction of these facilities and improving their efficiency once they were up and running.
In the following years, others have taken a similar approach to data center design. Microsoft has adopted data center modules in the facilities driving its web services.
In the past, as the company designed its modules, IO had no choice but to call on outside parts makers and manufacturers when it wanted to handle a physical prototype.
In recent months, it has started using a Makerbot 3-D printer to speed the process. Now, says vice president of engineering Zoll, it can prototype that light bracket in a couple of hours - “basically, over lunch time”.
“The beauty of the technology is that it takes the design of potentially complex objects - and the creation of these objects - and moves this away from specialized organizations, putting it into the hands of companies like ours, and individual people as well,” Zoll says.
It is worth noting that these are not full-size prototypes. IO’s data center modules are room-sized contraptions, and prototyping them in full would require an enormous printer. But Zoll can produce smaller models that mirror their basic design.
In the future, 3-D printing could be used to build not just prototypes but actual data center equipment.
“You can print things on a small scale to play with them. Architects do this all the time,” says Berok Khoshnevis, a professor of industrial and systems engineering at the University of Southern California who specializes in 3-D printing.
“But building a complete container would be a stupid thing to do. 3-D can’t give you the kind of quality that competing technologies give you.” Indeed, IO is only beginning to explore the possibilities of 3-D printing as a prototyping tool.