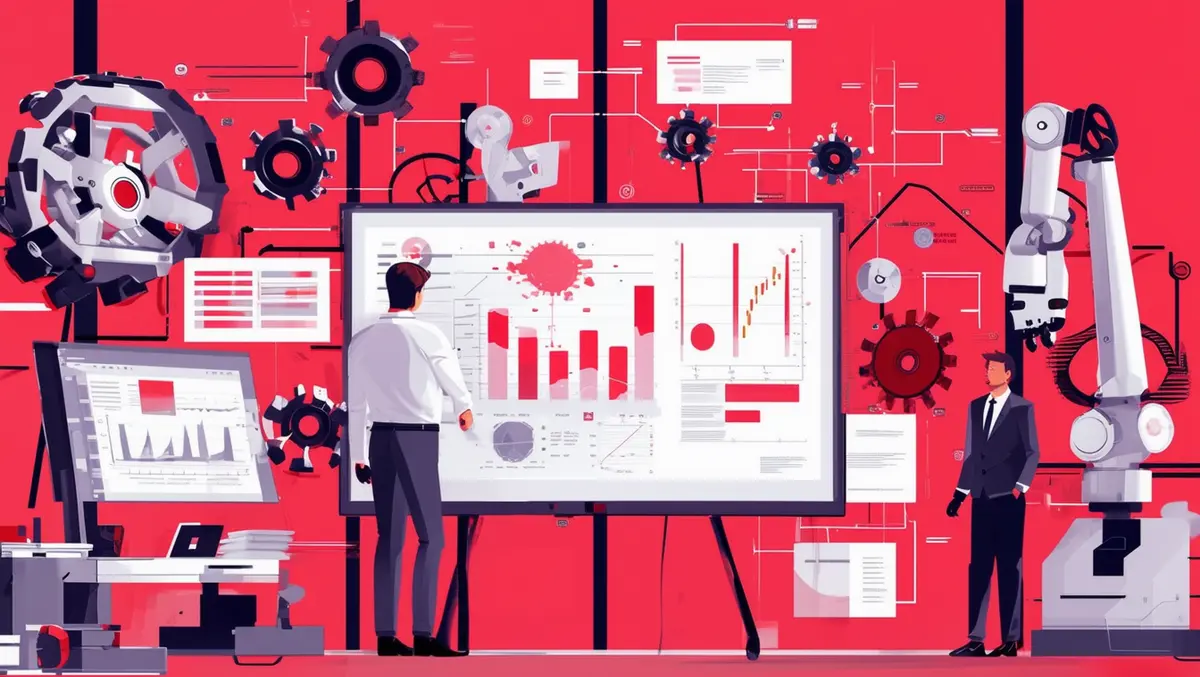
The three things businesses are getting wrong with automation
Intelligent automation has become a powerful tool that is revolutionising business operations. By streamlining processes, reducing errors, and enhancing overall efficiency, it allows companies to achieve new levels of productivity. But while automation offers significant potential, many organisations struggle to implement it effectively. We sat down with Ryan Stuchbery, General Manager – Automation at Avec, to explore the three most common mistakes companies make when introducing automation into their operations and how to avoid them.
Skipping the Operational Diagnostic
One of the biggest mistakes businesses make when implementing automation is diving in without first conducting a thorough diagnostic. This crucial step involves assessing the entire operational landscape to identify where automation can deliver the greatest value. Unfortunately, many organisations overlook this step, leading to misguided automation efforts that don’t address the most pressing needs.
“Not starting out with an operational diagnostic is the number one mistake”, says Ryan. “Businesses often jump straight to automating processes that seem like obvious pain points, without fully understanding the bigger picture. For example, companies may choose to automate tasks that are tedious or time-consuming based on employee complaints. However, just because a process is disliked doesn’t mean it’s the best candidate for automation.”
A comprehensive operational diagnostic helps businesses identify the processes that are best suited for automation by balancing employee pain points with overall impact on the business. This diagnostic process should involve mapping out all business processes, analysing the time and resources each one consumes, and evaluating which processes present the best opportunity for automation in terms of efficiency gains, error reduction, and overall business value.
Without this diagnostic, businesses risk automating the wrong processes – either overly complex ones with little return or simple, low-impact tasks that don’t provide significant benefits. The result is wasted resources and automation projects that fail to deliver on their promise.
Focusing solely on Full-Time Equivalent (FTE) augmentation
Another common mistake is placing too much emphasis on FTE uplift as the primary goal of automation. While enhancing capacity by freeing up human resources is often a key objective, it shouldn’t be the sole measure of success. Automation offers a wide range of benefits beyond just increasing capacity, and businesses that only focus on this aspect often miss out on other significant advantages.
According to Ryan, “there are a lot of other benefits to automation that should be weighed as well, such as plugging revenue leakage, enhancing regulatory compliance, and improving overall operational efficiency. For instance, automation can help companies identify and correct financial discrepancies, reduce errors in billing or payments, and ensure compliance with complex regulations more efficiently.”
However, many companies fail to consider these broader benefits for example, Ryan spoke to a project he had been involved with where the primary focus was on capacity uplift, leading to the selection of processes for automation that had minimal impact on overall operations. “Despite the investment in automation, ROI was limited because automation projects were selected based on an overall FTE value but in reality, that figure was made up of fractions of capacity from many individual resources. The small amount of time freed up for each individual prevented these resources from being redeployed onto other tasks and prevented the organisation from realising the benefit of their automations. This highlights the importance of taking a more holistic view of automation benefits.”
Reactive, not proactive, automation programs
Another mistake businesses often make is treating automation as a series of isolated projects rather than a continuous, strategic initiative. Companies frequently take a reactive approach to automation, implementing it in a response to immediate problems or specific pain points. While this can lead to short-term gains, it limits the long-term impact of automation efforts.
“The best automation programs are proactive rather than reactive,” Ryan emphasises. Proactive automation programs look beyond solving immediate issues and focus on building a sustainable automation pipeline. This involves continuously reviewing and optimising existing automation while also planning for future opportunities.
A proactive approach requires businesses to think strategically about their automation goals. What are the long-term objectives of the automation program? How does automation align with the company’s overall business strategy? What are the future opportunities for automation beyond the current set of processes? Answering these questions can help companies develop a roadmap for automation that delivers sustained value over time.
In contrast, reactive programs often fall into the trap of addressing only immediate pain points. This can lead to short-sighted decisions that limit the overall impact of automation efforts. A real-world example of this can be seen in the challenges faced by an automaton project the Avec team were a part of. The project encountered significant delays as client teams involved weren’t properly prepared or engaged from the outset. This lack of proactive planning slowed down the entire project and limited its effectiveness.
By taking a proactive approach to automation, businesses can build a robust pipeline of automation projects that deliver ongoing value. This involves not only identifying immediate opportunities for automation but also continually assessing the impact of existing automations and exploring new areas for improvement.
Where does Avec come in?
Automation holds tremendous promise for businesses of all sizes, but realising its full potential requires careful planning and execution. To avoid common pitfalls, businesses should focus on three key areas: conducting a thorough operational diagnostic, taking a holistic view of automation benefits, and adopting a proactive, long-term approach to automation.
For companies looking to improve their automation efforts, Ryan offers this advice, “Engage experienced partners with proven track records. Focus on the big picture – what are the strategic goals of your automation program, and how will you get there?” By aligning automation efforts with broader business objectives and continuously reviewing the impact of automation projects, companies can ensure they’re getting the most out of their investment.
Reach out to the Avec team today to align your automation efforts with your broader business objectives and ensure you’re getting the most out of your investment.